On Tuesday, Skoltech will host the grand opening of its newest state-of-the-art laboratory.
The Additive Manufacturing Laboratory, home to a globally unrivaled collection of the latest 3D printing technologies, will operate within Skoltech’s Center for Design, Manufacturing and Materials.
“We hope to prove our role as a core component of advanced manufacturing in Russia, as a link between industry and science. We understand the needs of the industry and are eager to conduct research in emerging areas,” said lab engineer Vladimir Kalyaev.
Senior engineer Vadim Stupnikov added: “In one lab, we have the full line of technology. We are able to prototype everything in plastic, and then recreate these prototypes in metal or ceramic. It’s rare to find a lab that offers all of these mediums, let alone one that has specialists on staff with expertise in working with all of them.”
He noted as well the intrinsically international nature of the facility: its equipment was sourced from as far afield as the Germany, France, South Korea, United States, and Japan, while its research staff hails from Russia, the United States and Chile.
A mammoth metal printer
The lab’s pride and joy is the Insstek MX 1000 – the biggest 3D printer in Russia, and one of only 15 such models on the planet.
The Insstek specializes primarily in printing large-scale parts from various types of metal to be used in the aviation, automotive, medical and space industries.
In addition to its size, one of the key attributes that sets the Insstek apart from other printers on the market is its capacity to make repairs directly within its printing chamber. If, for example, a turbine blade is chipped or cracked, the blade can be inserted into the chamber, and the Insstek can print material directly into the gap to fill it.
Stupnikov pointed out that the limits of the Insstek are not yet known; its developers are still working on finalizing its software, thus making it a hotbed for innovation.
To date, the Insstek has primarily worked with metal alloys, including steel, copper, aluminum, titanium and nickel.
The lab also features a Trumpf TruPrint 1000, a smaller-scale metal printer with a proven track record and solid global reputation for its ability to efficiently create components and parts from various types of metal.
For comparison, the Insstek boasts a rectangular printing chamber that measures 1,000 mm. by 800 mm. by 650 mm., while the Trumpf’s globular chamber has a diameter of 100 mm and a height of 100 mm.
The rise of the ceramic printer
The 3D Ceram Ceramaker 900 uses stereolithographic technology to print a broad array of ceramic materials, including zirconia, alumina, hydroxyapatite and more.
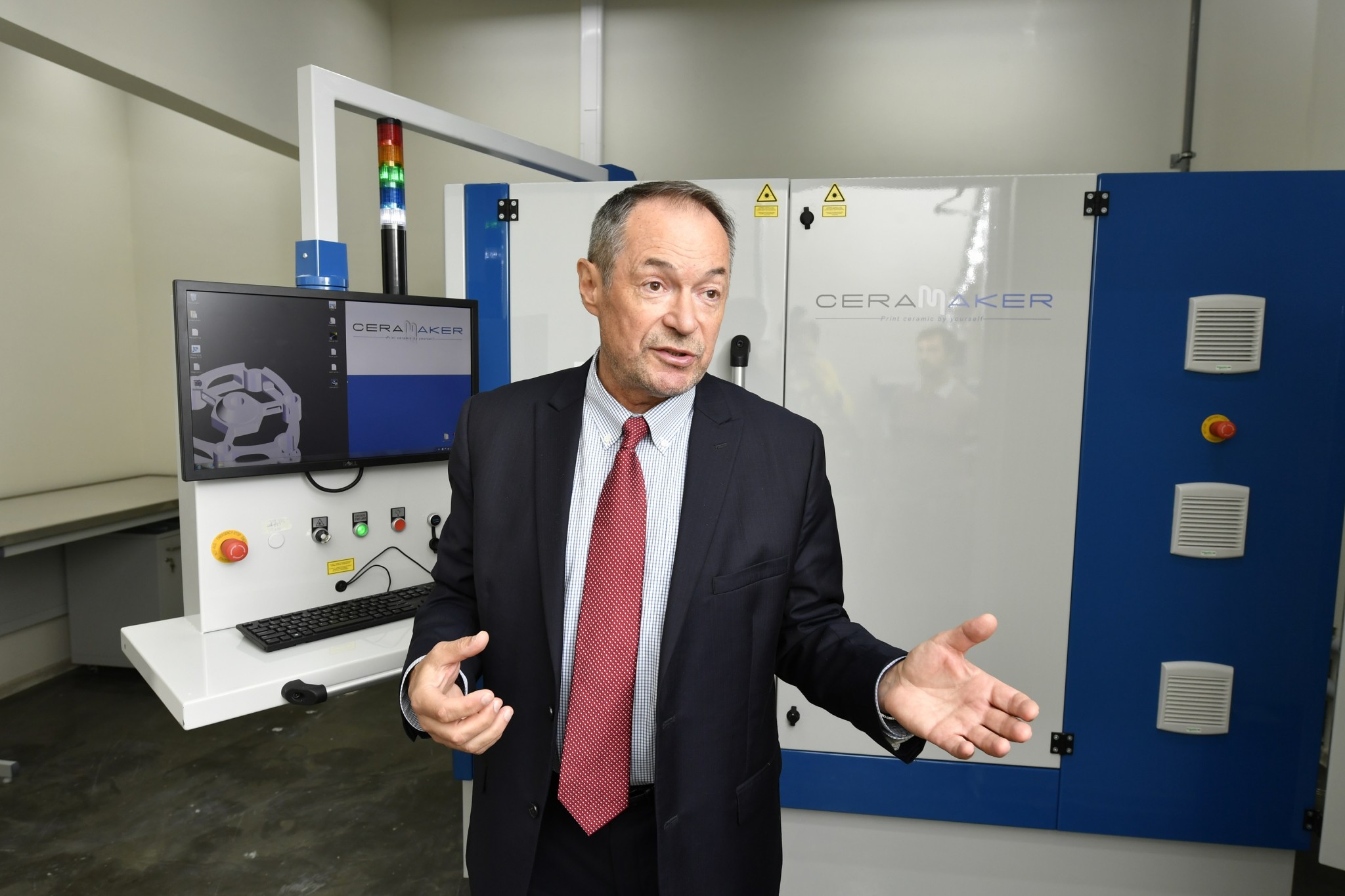
CDMM Director Iskander Akhatov pictured with the Ceramaker shortly after it was delivered to Skoltech in August 2017. Photo: Skoltech.
Ceramic is increasingly coveted in industries ranging from aerospace to medicine, and from electronics to fine jewelry. The Ceramaker can be used to accommodate the needs of all of the above – having printed everything from dielectric elements to cocktail rings.
Richard Gaignon, CEO of 3D Ceram, the French company that created Ceramaker, said he’s even received a request for a house printed from ceramic. This came as a particular shock in light of the fact that the average size of a Ceramaker product is 1 cm, Gaignon said during a recent visit to Skoltech.
In particular, it can be used to manufacture medical implants custom created to fit each patient’s individual parameters. This includes artificial joints and bone replacements.
According to Gaignon, of all of the projects his company has worked on, he is proudest of skull implants. “Manufacturing skull implants is really an achievement for 3DCeram. The technology makes it is quite complicated and on top of this, we needed to apply for very strict certifications in order to get [official] approval,” he said.
He added that the type of product most sought after by Ceramaker customers varies significantly by country.
“The most popular application is highly dependent on the country. In France and Switzerland, the jewelry market is quite strong. In Russia, the aircraft industry is quite important… each country has its own type of market,” said Gaignon.
Like the Insstek, the Ceramaker is extremely rare; according to Stupnikov, there are only about 30 currently in existence.
To supplement all of its 3D printing initiatives, the new Additive Manufacturing Lab’s researchers use a Plastic Projet printer to test the logistics of larger projects in advance using plastic.
Education and testing facilities
In addition to providing manufacturing services for industry, one of the laboratory’s chief goals will be that of promoting the use of 3D printing and technology in Russia. Among other things, this will include a wealth of facilities for clients wishing to test materials.
“If a company wishes to work with its own powder, we can test it and analyze the results using microscopy and stress machines,” he said.
The list of equipment for these purposes includes:
- The Accutom-100, a system that uses diamond, alumina or silicon carbide disks to grind and polish materials, and that can be used for a broad variety of analyses, including testing the microhardness and wear resistance of various materials;
- The TechPress2 and MetPrep3, a two-part sintering and polishing system that can prepare material samples for metallographic studies;
- High-Temperature Tribometer CSM Instruments, a system with a set of sensors that can be used to measure tangential force, angles, temperature and wear, enabling researchers to conduct experimental measurements of wear resistance, wear rates and friction coefficients;
- The Axio Scope.A1, an optical microscope that enables researchers to conduct microstructural characterizations of samples and analyze images with specialized image processing software.
“The Center for Design, Manufacturing and Materials’ MSc program includes a set of courses for advanced manufacturing. The Additive Manufacturing course is an important part of it. This course is organized with the ‘learning-by-doing’ concept in mind, so our students will actually design, manufacture and finally test new materials and products, gaining real experience in innovative engineering and science. We will be able to educate people on all of the most important and popular advanced manufacturing technologies in the world,” Stupnikov said.