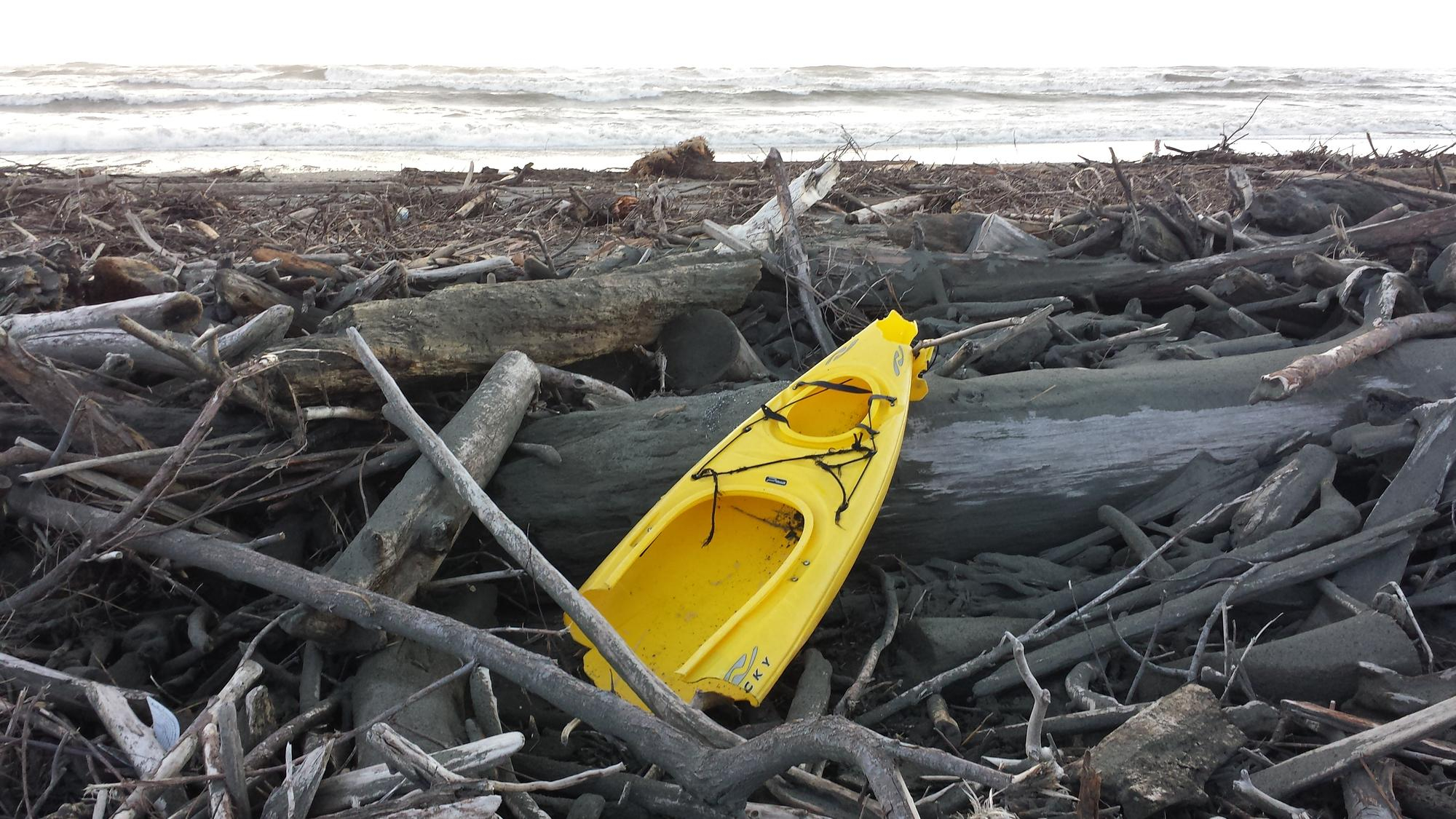
Broken kayak amid tree logs at a beach. Polymer parts of this kind are often reinforced with glass or carbon fiber, and their disposal poses problems for the environment
Skoltech researchers have demonstrated that reinforced plastics can be recycled without loss of original mechanical properties, sometimes even with improved characteristics. Published in Composites Communications, the study brings hope for an environmentally sounder — and economically viable — production of construction parts, car, aircraft, and marine vessel components, high-end sports equipment and other articles that currently end their service life in landfills.
Reinforced polymer composites are materials made of glass, carbon, or other fibers enveloped in a so-called polymer matrix, colloquially known as plastic. Depending on the polymer used as the matrix, these composite materials come in two basic types: Thermoset composites are heated during manufacture and then harden once and for all due to an irreversible chemical reaction. Thermoplastic composites, on the other hand, can be reheated and remolded, making them recyclable.
Skoltech scientists used thermoplastic composite rods, manufactured in a prior study, to explore how their mechanical properties deteriorate with repeated rounds of recycling. The rods were made of a polymer called polypropylene, reinforced with glass fibers. The team subjected the rods to compression molding, heating and pressing them into flat plates. The plates then underwent four rounds of recycling: Each time they were cut into strips, heated, and pressed into plates again. For each of the five “generations” of plates, mechanical tests determined their strength and elasticity.
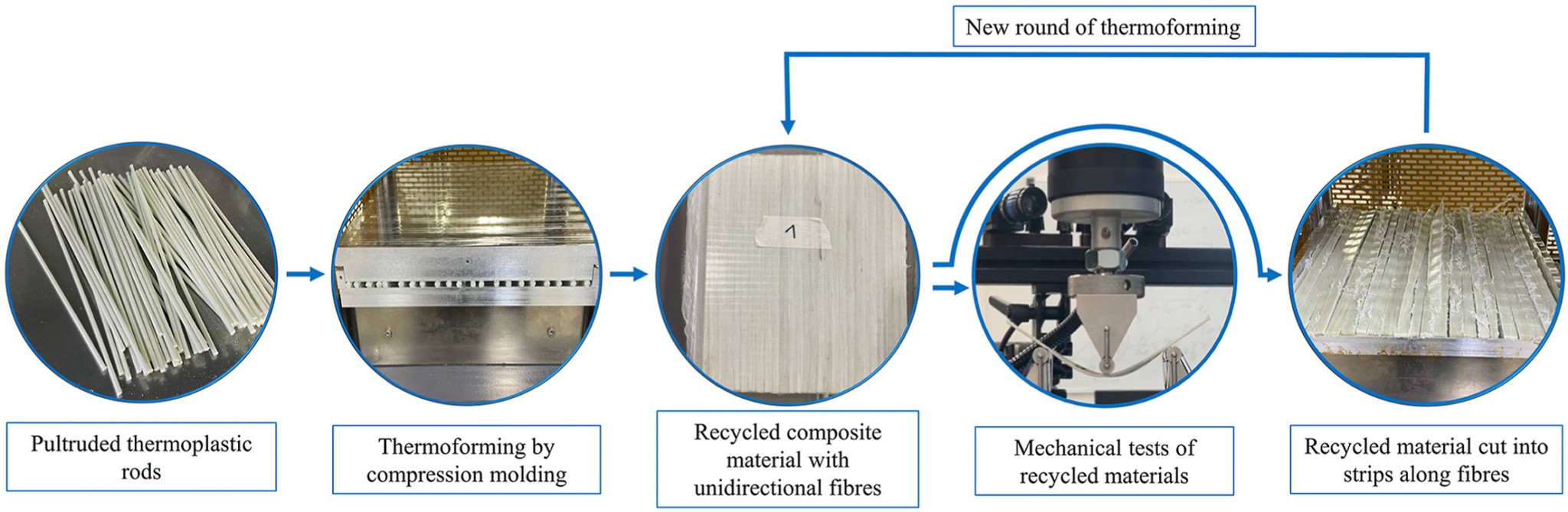
Basic layout of the study: glass fiber-reinforced polypropylene rods are heated and pressed into plates, which are then repeatedly cut into strips and pressed into plates again. The effects of such recycling on material properties are monitored. Credit: Valentina Kravtsova et al./Composites Communications
“What we found was that not only did the mechanical properties decrease slower than expected in the long run, but in fact, recycling occasionally improved them,” said the lead author of the study, Skoltech alumna Valentina Kravtsova, who graduated from the Advanced Manufacturing Technologies master’s program. “That improvement occurred at the initial recycling stage, when the item went from rod- to plate-shaped, followed by a relatively slow decline over the four subsequent rounds of plate-to-plate recycling.”
The researchers attribute these fairly encouraging results to the mode of recycling chosen. “The crucial part is you should not lose reinforcing fiber length. To recycle the plates, we cut them into stips along the direction of the fibers, which therefore mostly retained their length. Had we fractured or cut up the plates in a more arbitrary manner — as is often the case — every recycling round would entail a significant decrease in average fiber length, and that means worse mechanical properties,” commented the study’s principal investigator, Associate Professor Alexander Safonov from the Center for Materials Technologies.
As for the chemical composition of the material and its thermal properties, such as the melting point, they were also tested at various stages in the experiment and proved stable throughout the multiple rounds of recycling.
The implications of the team’s findings are that with proper incentives, fiber-reinforced thermoplastic composite materials could replace their poorly recyclable thermoset counterparts. Depending on source material quality and the precision of the recycling process itself, such parts can be repeatedly recycled without noticeably impairing their characteristics.
“Perhaps the first step that would be the easiest to implement is to apply compression molding immediately to any just-manufactured items found to have defects, reforming them into articles of different shapes with superior properties. This is analogous to when rods were first pressed into plates in our study,” Skoltech doctoral student Kirill Minchenkov from the Mathematics and Mechanics PhD program, who co-authored the study, added. “Recycling used products instead of discarding them, as it happens today with thermoset polymer-based composites, would be the next step.”
Contact information:
Skoltech Communications
+7 (495) 280 14 81